- Concrete Mix Design
- Fineness Modulus Method
- Materials and Methodology
- Materials
- Methodology
- Specific Gravity Test
- Specific Gravity for Coarse Aggregate
- Specific Gravity for Fine Aggregate
- Water Absorption Test
- Water Absorption Test for Coarse Aggregate
- Water Absorption Test for Fine Aggregate
- Test on Workability (Slump Test)
- Measurement of workability
- Slump Test
- Zoning Test on Fine Aggregate
- Grading Test on Coarse Aggregate
- Calculations
- Conclusion
Concrete Mix Design

Concrete mix design calculation can be characterized as the way toward choosing appropriate elements of concrete and deciding their relative proportions with the object of creating concrete of certain minimum durability and strength as economically as possible. One of the definitive points of contemplating the different properties of concrete materials, hardened concrete and plastic concrete is to empower the concrete technologists to design a mix concrete for specific for specific durability and strength.
Sometimes the site engineer might be needed to marginally adjust the mix proportions given by the mix designer. The engineer also sometime makes cylinders and cubes and tests them to affirm the accomplishments concerning the minimum determined strength for the concrete mix design calculation. Concrete mix designer, prior may have trial cubes with representative materials to show up at the worth of coefficient of variation or standard deviations of variety to be utilized in mix design.
The first object is to achieve the required minimum strength, the second object is to achieve the required minimum durability and the third object is to make the concrete in most economical matter.
Here it is discussed about the concrete mix design calculation, Fineness modulus, materials and methodology for concrete mix design calculation, specific gravity test of concrete mix design calculation, water absorption test of concrete mix design calculation and slump test for concrete mix design calculation and the concrete mix design numerical.
Fineness Modulus Method
This law states that when concrete is fully compacted, its compressive strength is inversely proportional to the water / cement ratio. For the purpose of applying this law, concrete can be considered as fully compacted, if it contains less than 2% of air voids. According to Abrams, the 28 days compressive strength of concrete is given by,
S = K1 / (K2) x
Where, K1 and K2= empirical constants equals to 700 and 3.5 respectively.
x = water/cement ratio by volume
S = concrete’s compressive strength in kg/cm2
A new method of mix-proportioning was suggested by Abrams, in which the workability was assessed in relation to a new property of the aggregate, designated as “Fineness Modulus” which is a measure of mean size of particles in the entire body of aggregates. The Fineness Modulus is obtained as a sum of cumulative percentage retained on a set of standard sieves. The proportion of fine to coarse aggregate is dependent on the richness of cement content in the mix is given by the formula,
P = 100 (A-B) / (A-C)
Where, P = the percentage of fine aggregate by weight of the total aggregate
A = coarse aggregate’s fineness modulus
C = fine aggregate’s fineness modulus
B = the maximum fineness modulus permissible depending upon the quantity of cement used and the maximum size of aggregate.
The major drawback of this method is that it is possible for aggregates to have substantially different grading and yet have the same fineness modulus, requiring the number of trail mixes to achieve the desired workability.
The early mix design procedures discussed above may be considered to have paved the way for better insight into the field of concrete mix design and they have also indicated the importance of the various parameters influencing the concrete mix. The subsequent investigators realized the importance of practical approach in formulating the mix design procedures since the parameters involved are such that they are not easily amenable for theoretical postulations. Most of the mix design methods which are popular at the present day are invariably based on extensive experimental investigations.
Materials and Methodology
Materials
The materials used in the concrete mix design calculation are:
- Cement: OPC-43 grade, Max brand, bought from the local market.
- Coarse Aggregate: Locally available crushed angular aggregate from Kling area Plant, Meghalaya.
- Fine aggregate: Locally available graded fine aggregate falling in Zone-IV.
- Water: Potable water from college bore pump.
- Admixture: No admixture used in this Mix-design.
Methodology
There are several methods to fulfill the concrete mix design calculation. They are listed below.
Specific Gravity Test
In concrete mix design calculation specific gravity of aggregate is additionally needed in figuring the compacting factor regarding the workability measurement. Additionally, specific gravity of aggregate is needed to be viewed as when we manage heavy weight and light weight concrete. Average specific gravity of the rocks varies from 2.6 – 2.8.
Aggregates are inert ingredients that occupy nearly 70 – 75% volume of concrete. The physical, chemical and thermal properties influence the properties and performance of concrete. The specific gravity is one of the important physical properties of aggregate. The dry aggregate can affect the workability and water-cement ratio of the mix.
Specific Gravity for Coarse Aggregate
Aim: Determining the specific gravity of coarse aggregate.
Apparatus Required:
- Pycnometer
- Dry Aggregate
- Water
Procedure:
- Take Natural dry clean sample.
- Take the weight of vessel as (W1).
- Now, note down the weight of pycnometer with sample and water (W2).
- Take the weight of pycnometer with sample and water (W3) .
- Take the weight of pycnometer with water inside it (W4).
- Now, calculate the specific gravity of coarse aggregate.
It is given by,
GCA = (W2 – W1) / [(W2 –W1) – (W3 –W4)]
Where, W1 = empty weight of pycnometer.
W2 = sample+weight of pycnometer
W3 = weight of pycnometer + sample + water.
W4 = weight of pycnometer + water.
Specific Gravity for Fine Aggregate
Aim: Determining the specific gravity of fine aggregate.
Apparatus Required:
- Pycnometer
- Water
- Aggregates
Procedure:
- Take clean sample of aggregates.
- Take the weight of vessel as (W1).
- Take the weight of pycnometer with sample (W2) .
- Take the weight of pycnometer with sample and water (W3) .
- Take the weight of pycnometer with water only (W4) .
- Now, calculate the specific gravity of the given sample.
It is given by,
GFA = (W2 – W1) / [(W2 – W1) – (W3 – W4)]
Where, W1 = empty weight of pycnometer
W2 = sample+weight of pycnometer
W3 = weight of pycnometer + sample + water
W4 = weight of pycnometer + water.
Water Absorption Test
The idea of strength of aggregate can be assumed by the water absorption test. Aggregates having more water absorption are more porous in nature and are for the most part viewed as inadmissible except if they are discovered to be satisfactory dependent on impact, hardness and strength test. Some aggregates are generally porous and absorptive. In concrete mix design calculation the water-cement ratio and the workability of concrete will be affected by porosity and absorption of aggregate. The porosity of aggregate will also affect the durability of concrete when it is subjected to freezing and thawing and also when the concrete is subjected to chemically aggressive liquids.
To determine the water absorption of aggregate the sample is oven dried for 24 hours and then measured the increase of weight after the period. The ratio of increase in the weight to the weight of dry sample expressed as percentage is known as absorption of aggregate. The aggregate absorb water in concrete and thus affects the workability and final volume of concrete. The absorption capacity of coarse aggregate is about 0.5 to 1 percent by weight of aggregate.
Water Absorption Test for Coarse Aggregate
Aim: Determining the water absorption of coarse aggregates.
Apparatus Required:
- Aggregate (200gm)
- Water
- Oven
- Weighing machine
Procedure:
- Take dry sample of 200gm (W1).
- Merge it in water for 24 hrs.
- Wipe the sample with a clean cloth to remove the extra water.
- Weight the aggregate and note it down as (W2).
- Put it into the oven for 24 hours at 105°C – 110°C.
- After oven drying take the sample weight (W3).
It is given by,
WFA = [(W2 – W1) / W1]x 100
Where, W1=weight of dry sample
W2=Weight of wet sample
Water Absorption Test for Fine Aggregate
It is given by,
WFA = [(W2 – W1) / W1] x 100
Where, W1 = weight of dry sample
W2 = Weight of wet sample
Test on Workability (Slump Test)
The factors affecting workability are:
- water content
- mix proportions
- size of aggregate
- shape of aggregate
- surface texture of aggregate
- grading of aggregate
- Use of admixture
Measurement of workability
The Following test are commonly use to measure workability:
- Slump test
- Compacting factor test
- Flow test
- Kelly ball test
- Vee-Bee Consistometer test
Slump Test
In slum test the apparatus used is a metallic mould like a frustum of a cone which have the internal dimensions as given below,
- Bottom diameter : 20cm
- Top diameter : 10cm
- Height : 30cm
- Thickness : should not be thinner than 1.6mm
In slump test for concrete mix design calculation the concrete is tamped by a steel tamping rod 16mm diameter and 0.6 m long. The mould is then filled in four layers, each approximately ¼ of the height (30/4 = 7.5cm) of the mould. The layers of concrete filling is tamped 25 times after each layer. This allows the concrete to subside.
The concrete volume for slump cone test is obtained by,
Volume of frustum = [πh / 3(R2 + Rxr + r2)] = [3.14 × 0.3 / 3 (0.12 + 0.1 x 0.05 + 0.052)] = 0.0055 cum
Where, R = radius of lower base
r = radius of upper base
h = height
The slump obtained is 50mm.
Zoning Test on Fine Aggregate
Aim: To decide the zone of fine aggregate.
Procedure:
- Take clean sample of 1kg.
- The sample of aggregate is passed through 10mm, 4.75 mm, 2.36 mm, 1.18 mm, 600 micron, 300 micron and 150 micron sieves.
- Take the weight of aggregates retained on these sieves.
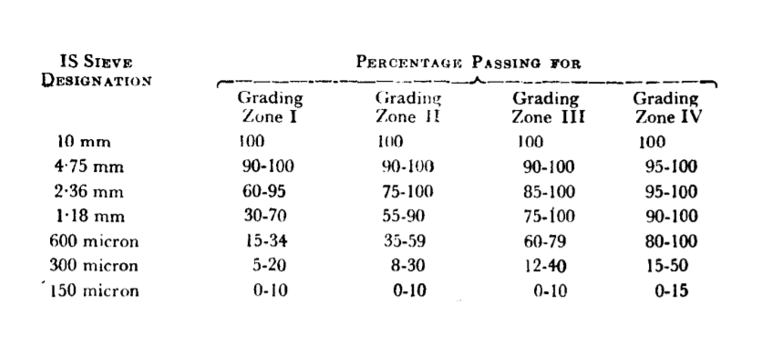
Observation Table and Calculation:
IS Sieve size (mm) | Weight of the aggregate retained (g) | Percentage weight retained | Cumulative Percentage retained | Percent Finer |
1) 10mm | 0 | 0 | 0 | 100 |
2) 4.75mm | 0.12 | 0.012 | 0.012 | 99.988 |
3) 2.36mm | 15.90 | 1.59 | 1.602 | 98.398 |
4) 1.18mm | 20.40 | 2.04 | 3.642 | 96.358 |
5) 600mm | 121.00 | 12.1 | 15.742 | 84.258 |
6) 300mm | 376.1 | 37.61 | 53.352 | 46.648 |
7) 0.15mm | 346.40 | 34.64 | 87.992 | 12.008 |
8) Pan | 77.10 | 7.71 | 95.702 | 4.298 |
Total | 258.044 |
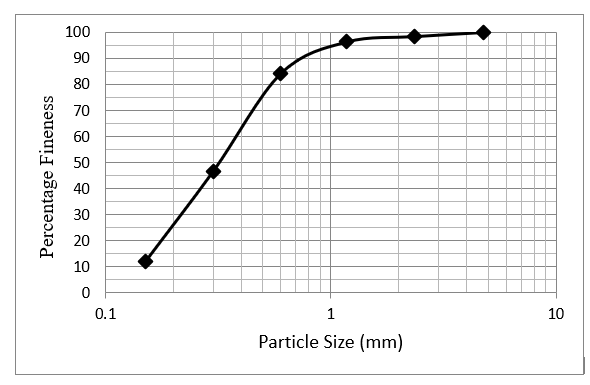
Grading Test on Coarse Aggregate
Aim: To determine grading zone of coarse aggregate.
Procedure:
- Take clean sample of 5kg.
- Pass it through 40 mm, 20mm, 10mm, and 4.75mm sieves.
- Take the weight of aggregates retained on these sieves.

Observation Table and Calculation:
IS Sieve Size (mm) | Particle size (mm) | Weight of aggregate Retained (g) | Percentage weight retained | Cumulative percentage retained | Percent finer |
40mm | 40 | 0 | 0 | 0 | 100 |
20mm | 20 | 338.8 | 33.82 | 33.82 | 66.18 |
10mm | 10 | 634.5 | 63.45 | 97.27 | 2.73 |
4.75mm | 4.75 | 12.1 | 1.21 | 98.48 | 1.52 |
Total | 229.57 |
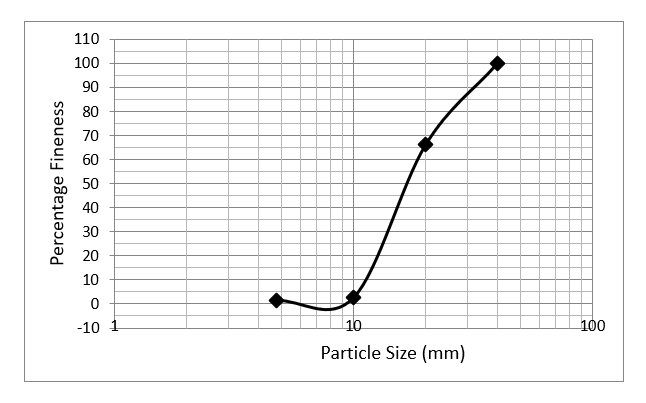
Calculations
There are many calculations in mix design calculation for concrete. The concrete mix design calculation for the mix design of M35 grade of concrete are:
Specific Gravity Test
(a) Coarse Aggregate
Let, W1 = empty weight of pycnometer.
W2 = sample+weight of pycnometer
W3 = weight of pycnometer + sample + water.
W4 = weight of pycnometer + water.
Here,
- W1 = 519 g
- W2 = 1235.8 g
- W3 = 1958.9 g
- W4 = 1521.3 g
GCA = (W2 – W1) / [(W2 – W1) – (W3 – W4)]
= (1235.8 – 519) / [(1235.8 –519) – (1958.9 –1521.3)]
= 2.57
(b) Fine Aggregate
GCA = (W2 –W1) / [(W2 –W1) – (W3 –W4)]
Where, W1 = empty weight of pycnometer
W2 = sample+weight of pycnometer
W3 = weight of pycnometer + sample + water
W4 = weight of pycnometer + water.
Here,
- W1 = 519 g
- W2 = 866.3 g
- W3 = 1718.4 g
- W4 = 1518.2 g
GCA = (W2 –W1) / [ (W2 –W1) – (W3 –W4) ]
= (866.3–519) / [(866.3–519) – (1718.4–1518.2)]
= 2.36
Water Absorption Test
(a) Coarse aggregate
It is given by,
WCA = [(W2 – W1) / W1] x 100
Where, W1 = weight of dry sample
W2 = weight of wet sample
Therefore, WCA = [(W2 – W1) / W1] x 100
= [(91.31–91)/91.31] x 100
= 0.34%
(b) Fine aggregate
It is given by,
WFA = [(W2 – W1) / W1 ] x 100
Where, W1 = weight of dry sample
W2 = Weight of wet sample
Therefore,
WFA = [(W2 – W1) / W1 ] x 100
= [(100.69–100)/100.69] x 100
= 0.69%
Workability Test (Slum Test)
The slump obtained is 50mm.
Mix Design
- Stipulations for Design
Design of concrete mix for M35 Grade of Concrete with following data:
Type of Cement = OPC 43
Maximum size of aggregate = 20mm
Exposure condition = Severe (RCC)
Workability = 50mm slump
Minimum Cement Content = 340 kg/m3
Maximum Water/Cement Ratio = 0.45
Degree of supervision = Good
Type of aggregate = Crushed Angular Aggregate
- Data for Testing of Materials
Specific Gravity of Coarse Aggregate = 2.57
Specific Gravity of Fine Aggregate = 2.36
Water absorption of Coarse Aggregate = 0.34 %
Water absorption of Fine Aggregate = 0.69 %
Grading of Coarse Aggregate confirming to 20 mm nominal size.
Grading of Fine Aggregate confirming to grading Zone IV.
- Target Mean Strength
Characteristic Strength, f ck = 35
The Target Mean Strength (f ‘ck) is determined as f ck + 1.65 + S = 35 + 1.65 + 5 = 41.65 N/mm2
Where, S = standard deviation taken as 5 N/mm2.
- Water / Cement Ratio
Water / Cement Ratio = 0.38 (based on experience)
- Selection of Water Content
As per nominal maximum size of aggregate that is 20mm, the maximum water content is 186 liter. This is for 50mm slump.
- Calculation Of Cement Content
Water / Cement Ratio = 0.38
Water used = 186 liters
Therefore, Cement Content = W / C = 0.38
C = 186 / 0.38 = 489.47 kg / m3
Since, the value of Cement Content is 489.47 kg / m3 i.e. more than 340 kg / m3.
Therefore, we will adopt cement = 489.47 kg / m3.
- Calculation of Coarse and Fine Aggregate Content
Volume of Coarse aggregate corresponding to 20mm size aggregate and fine aggregate Grading Zone IV, for water cement ratio is found out to be 0.66.
But in present case we are considering W / C ratio as 0.38.
Here, 0.5 – 0.38 = 0.12
Therefore it is less by 0.12.
The Coarse aggregate is increased at a rate of 0.01 for every decrease in W / C Ratio of 0.05.
Here, (0.01 / 0.05) x 0.12 = 0.024
Volume of Coarse aggregate = 0.66
Therefore, corrected proportion of volume of CA = 0.66 + 0.024 = 0.684 = 0.68 (approx.)
Therefore, Coarse aggregate volume = 0.68
Fine aggregate volume = 1 – 0.68 = 0.32
- Calculation of Mix Proportions
Volume of Concrete = 1 m3
Absolute Volume of Cement = (489.47/3.15) × (1/100)= 0.155 m3
(The specific gravity test for cement is not done and is assumed as 3.15 for calculations.)
Volume of water = 186 liters = 0.186 m3
Now, all the materials absolute volume except,
Total aggregates = 0.155 + 0.186 = 0.341 m3
Absolute volume of total aggregates = 1 – 0.341 = 0.659 m3
Now,
Weight of Coarse Aggregate = 0.659 x 0.68 x 2.57 x 1000 = 1151.67 kg / m3
Weight of Fine Aggregate = 0.659 x 0.32 x 2.36 x 1000 = 497.68 kg / m3
- Mix Proportions for Trial No. 1 (SSD Condition)
Cement = 489.47 kg / m3
Water = 186 kg / m3
Fine Aggregate = 497.68 kg / m3
Coarse Aggregate = 1151.67 kg / m3
Wet Density of Concrete = 2324.82 kg / m3
Water / Cement Ratio = 0.38
- Site / Field Correction
Absorption of Fine Aggregate = 0.69 % = (0.69/100) x 497.68 = 3.43 liters
Absorption of Coarse Aggregate = 0.34 % = (0.34/100) X 1151.67 = 3.91 liters
Therefore, total absorption = 3.43 + 3.91 = 7.34 liters
Therefore, the actual amount of water to be used = 186 + 7.34 = 193.34 liters
Actual Weight of Fine Aggregates to be used = 497.68 – 3.43 = 494.25
Actual Weight of Coarse Aggregate to be used = 1151.67 – 3.9 = 1147.76
Therefore, proportions of materials at the site are:
Cement = 489.47 kg / m3
Water = 193.34 kg / m3
Fine Aggregate = 494.25 kg / m3
Coarse Aggregate = 1147.76 kg / m3
- To Express the Proportion in Trial No. 1 (SSD Condition)
Cement Fine Aggregate Coarse Aggregate Water
489 498 1152 186
1 1.01 2.36 0.38
- To Express the Proportion in Field / Site Condition
Cement Fine Aggregate Coarse Aggregate Water
489 494 1148 193
1 1.01 2.35 0.39
- Compressive Strength of 7 and 28 Days
7 Days mean compressive strength of concrete:
Sample No. | Area (mm2) | Load Taken (kN) | Compressive Strength (N/mm2) |
1 | 100 x 100 = 10000 | 550 | 24.44 |
2 | 100 x 100 = 10000 | 23.11 | 23.11 |
3 | 100 x 100 = 10000 | 23.55 | 23.55 |
28 Days mean compressive strength of concrete:
Sample No. | Area (mm2) | Load Taken (kN) | Compressive Strength (N/mm2) |
1 | 150 x 150 = 22500 | 790 | 35.11 |
2 | 150 x 150 = 22500 | 800 | 35.56 |
3 | 150 x 150 = 22500 | 760 | 33.78 |
Conclusion
From the concrete mix design calculation for M35 design experimental study, the following important points are noted for the M35 Concrete Mix Design as:
- 7 days mean compressive strength was found to be 23.70 N/mm2 (It should be @75 percent of 35 N/mm2 = 26.25 N/mm2).
- 28 days mean compressive strength was found to be 34.82 N/mm2 (It should be @ 100% of M35 = 35N/mm2).
- The difference in mean compressive strength of 7 days = (26.25-23.70) = 2.55 N/mm2 (91.29%).
- The difference in mean compressive strength 28 days = (35.00-34.82) = 0.18 N/mm2 (99.49%).
It may be concluded that in the concrete mix design calculation the mean compressive strength after 7 and 28 days of curing is found out to be 23.70 N/mm2 and 34.82 N/mm2 respectively, which is less than the required strength of M35. The possible errors caused may be due to the following reasons:
- Inadequate and improper curing of cubes: As it was found that the curing tank was emptied by some unknown miscreants and also in some instances 2-3 numbers of the cubes was found to be out of the tank.
- Fault in CTM calibration: As during testing of cubes it was found that the two numbers after 28 days cured cube was back from 800 kN marking but the maximum range of CTM is 1000 kN.
- Inefficiency in testing of constituent materials: To err is human. So, there may be possible crept of error during testing of the physical properties of the constituents of the mix.
- Inadequate compaction during casting of cubes: It was found in first trial of cubes the compressive strength after 7 days was found to be very-very less than the desired result though we use the same materials and mix design. Later test was found to be nearest to the desired strength but with few exceptions.
- Prescribed minimum slump and achieved slump: The slump achieved during test was found to be 0 (zero) but as in M35 design the minimum slump to be used was 50mm.
- Time constraint: The time stipulated and with the work load of daily classes, exam, programs of college, holidays, etc. leads to constraint of time.
This study gives useful insight about the concrete mix design calculation to achieve the targeted mean strength.