Concrete
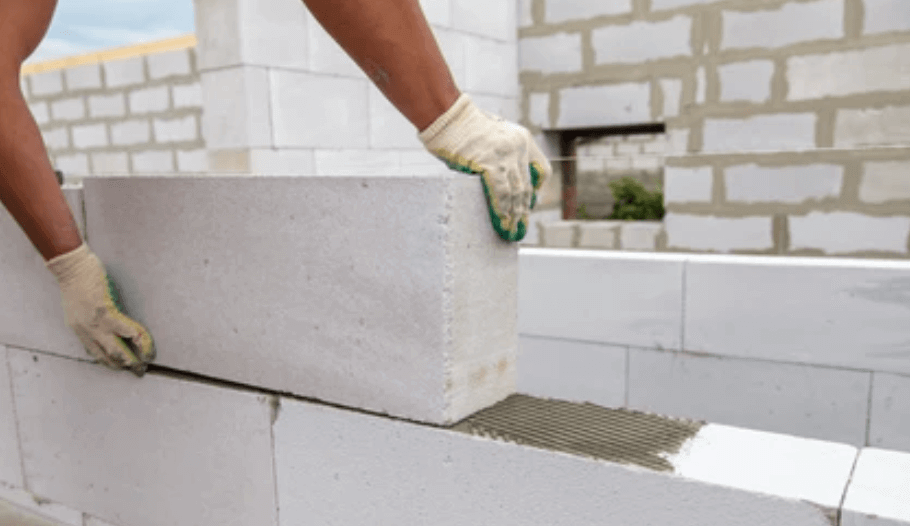
Concrete is a composite material which is produced using a mixture of cement, aggregate, water and some of the time admixtures are utilized in required extents. It is quite possibly the most significant and valuable materials for construction work. At the point when every one of the fixings like, cement, aggregate, water and admixtures are mixed in required extents, the cement and water start a reaction with one another to tie themselves into a solidifies mass. The solidifies rock lime mass is known as concrete.
Concrete is affordable than other structure materials. The compressive strength of concrete is exceptionally high and it is extremely impressive in compression. It very well may be cast effectively into any ideal shape and has a base corrosive and weathering impacts. The concrete made with steel reinforcement gives equivalent coefficients of warm development and it is fire safe. It tends to be pumped and sprayed in troublesome positions. The concretes are extremely long sturdy and have a little upkeep cost which can be disregarded.
Foam Concrete
Foam concrete is also called as lightweight concrete that is made from water, sand or fly ash, cement, and foam. Foam concrete or the lightweight concrete can be characterized as a cementitious material that comprises of least 20% of foam, that is precisely entrained into the plastic mortar. The dry density of foamed concrete might differ from 300 – 1600 kg/m3.
The compressive strength of not set in stone at 28 days, goes from 0.2 – 10 N/mm2 or can go higher. Foam concrete is separated from air entrained concrete as far as the volume of air that is entrained. The air entrained concretes takes in the air of up to 3% – 8%. It additionally varies from the impeded mortar and aerated concrete for a similar explanation of level of air entrained. On account of hindered mortar systems, it is 15% – 22%. The bubbles are chemically framed on account of an aerated concrete.
Production of Foam Concrete

The foamed concrete or the lightweight concrete comprises surfactant dilution in the water for the production, which will be passing through a foam generator that produces the foam of stable structure. In the cementitious mortar or the grout the foam produced is mixed in it, so as to produce the foamed quantity of required density. These surfactants are likewise utilized in the assembling of low-density fills.
These are likewise called as Controlled Low Strength Material (CLSM). The foam is added straightforwardly to mix of rich sand and low cement content to acquire an air content of 15% – 25%. It should be remembered that low density fillers are provided as foamed concrete or lightweight concrete by certain producers, so deceptive should be taken consideration. Two principle methods are utilized for production of foamed concrete:
- Inline Method
- Pre-foam Method
Inline Method of Foam Concrete Production
The base mix of sand and cement is added to a unit. In this unit, the mix is mixed with foam completely. The most common way of mixing is completed with appropriate control. This will help in mixing of bigger amounts. The inline method involves two cycles, such as,
- Wet Method – Inline System
- Dry Method – Inline System
Wet Method of Inline System: The materials utilized in the wet method will be wetter in nature. With the assistance of a progression of static inline mixers, the base material and the foam are taken care of and mixed together. The persistent on-board density monitor is utilized to really look at the mixing of the entire mix. The output volume is subject to the density of the foamed concrete and not on the prepared mixed truck; that is one 8.0 m3 conveyance of base material which will produce 35 m3 foam concrete of 500 kg/m3 density.
Dry Method of Inline System: The dry materials for the production are utilized here. They are accepted into the silos. From here they are weighed appropriately and mixed with the assistance of on-board mixers. Then, the mixed base materials are pushed or pumped to a mixing chamber. Foam is added and mixed in wet method of foam concrete production. This method utilizes a lot of water for mixing. 130 m3 of foamed concrete or lightweight concrete can be produced from a solitary conveyance of cement or fly ash mix.
Pre-Foam Method of Foam Concrete Production
Here, the prepared mix truck carries the base material to the site. Through the opposite finish of the truck, the pre-framed foam is infused into the truck, while the mixer is turning. Along these lines, little amounts of foam concrete can be produced for little works, as for grouting or trench fill works. This method would give foam concrete densities going from 300 – 1200 kg/m3. The foam information will be from 20 – 60 rate air.
The last volume of the foam can be determined by decreasing the measure of other base material. As this is done in the truck. Control of stable air and density is hard for this method. In this way, a level of under and over yield should be determined and allowed. At the point when the foam is shaped, it is joined with a cement mortar mix having water cement proportion of 0.4 – 0.6. On the off chance that the mortar is wet, the foam becomes unstable. In case it is too dry, the pre-foam is hard to mix.
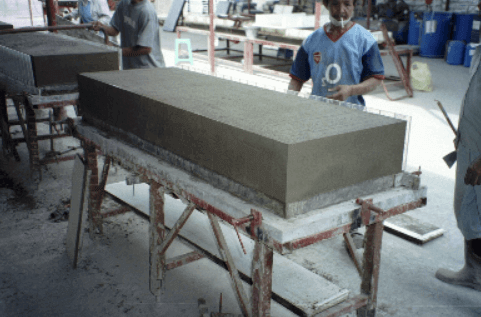
Materials for Foam Concrete
Cement for Foam Concrete
Ordinary Portland cement is regularly utilized, however quick solidifying cement can likewise be utilized if essential. Foam concrete or lightweight concrete can consolidate a wide scope of cement and other mix, for instance, 30% of cement, 60% of fly-ash and limestone in 10%. The substance of cement goes from 300 – 400 kg/m3.
Sand for Foam Concrete
The most extreme size of sand utilized can be 5.0 mm. Utilization of finer sands up to 2.0 mm with sum going through 600 microns sieve ranges from 60% – 95%.
Foam
The hydrolysed proteins or the synthetic surfactants are the most well-known structures dependent on which foams are made. The synthetic based foam agents are simpler to deal with and are modest. They can be put away for a more extended period. Lesser energy is needed to produce these foams. The protein-based foam is exorbitant however have high strength and performance.
There are two types of foam i.e., dry foam and wet foam. Wet foams with densities lesser than 100 kg/m3 are not suggested for the assembling of foam concrete. They have a freely place enormous bubble structure. The agent and the water are being sprayed into a fine mesh. This interaction produces foam that has bubbles with size going from 2.0 – 5.0 mm.
Dry foam is exceptionally stable in nature. An answer of water and the foaming agent is forced by limitations into a mixing chamber by compressor air. The produced foam has bubble size which is more modest than the wet foam. That is under 1.0 mm. These give a design of bubbles, which are equally orchestrated. The foaming admixtures are covered in the BS 8443: 2005.
Pozzolanas for Foam Concrete
The beneficial cementitious materials like fly ash and ground granulated blast furnace slag have been utilized broadly in the production of foam concrete or lightweight concrete. The measure of fly ash utilized reaches from 30% – 70%. The White GGBFS ranges from 10 to half. This lessens the measure of cement utilized and prudent. Silica fume can be added to build the strength at a measure of 10 rate by mass.
Other Materials for Foam Concrete
The coarse aggregate or other replacement for coarse can’t be utilized. This is on the grounds that these materials would soak in the lightweight foam.
Composition of Foam Concrete
Foamed concrete or the lightweight concrete composition changes with the density that is request. By and large, the concrete foam or lightweight concrete that has densities less than 600 kg/m3 will have foam, water, cement likewise some expansion of limestone dust or fly-ash. Sands can be utilized to accomplish higher density for foam concrete. The base mix is 1:1 – 1:3 for heavy foam concrete or lightweight concrete, which is filling product to Portland Cement proportion (CEM-I). For additional densities, say more noteworthy than 1500 kg/m3 more filler and medium sand is utilized. To decrease the density, the filler sum ought to be diminished. It is prescribed to wipe out the foam concrete with density lesser than 600 kg/m3.

Mix Details of Foam Concrete
The foam concrete properties rely on the following variables:
- The volume of foam
- The cement-content in mix
- The filler materials
- The ages
The impact of water cement proportion affects the properties of the foam concrete or lightweight concrete, not at all like foam and the cement content.
Properties of Foam Concrete
Visual Appearance of Foam Concrete
The specific comparison for the foam that is fabricated to produce foam concrete takes after the shaving foam. At the point when this is mixed with the mortar of standard determination, the last mix will take after the consistency of milkshake or yogurt.
Hardened Properties of Foam Concrete
The actual properties of the foam concrete are unmistakably identified with the dry density. The warm conductivity of foam concrete reaches from 0.1 W/mk – 0.7 W/mk. The drying shrinkage goes from 0.3% – 0.07% at 400 and 1600 kg/m3 separately. The foamed concrete or lightweight concrete doesn’t have an identical strength like an autoclaved block with comparable density.
Under the activity of load, there is inward hydraulic pressure made inside the design, which would cause the twisting of the foam concrete or lightweight concrete. The solidified foam concrete has great obstruction against freezing and thawing. It was seen that the use of foamed concrete in a space of temperature going from -18 degree Celsius to +25 degree Celsius gave no indications of harm. The density of foamed concrete utilized here range from 400 – 1400 kg/m3.
Fresh Properties of Foam Concrete
The workability of foamed concrete is exceptionally high and have a slump worth of 150 mm to collapse. These have a solid plasticizing impact. This property of foam concrete makes it exceptionally requested in the majority of the applications. When the flow of the mix has stayed static for a more drawn out period, it is undeniably challenging to restart its unique state. The odds of bleeding in foamed concrete are diminished because of high air content.
At the point when the mix temperature builds, great filling, and contacts are completed because of the development of air. In the event that the measure of sand utilized is higher or coarse aggregates is utilized other than the standard determinations, there are opportunities for segregation. This can likewise prompt the collapse of the bubble, which would decrease the complete volume and the foam structure. It is fine to do pumping of fresh foam concrete with care. Towards the end with turbulence, the free of foam concrete or lightweight concrete may bring the collapse of bubble structure.
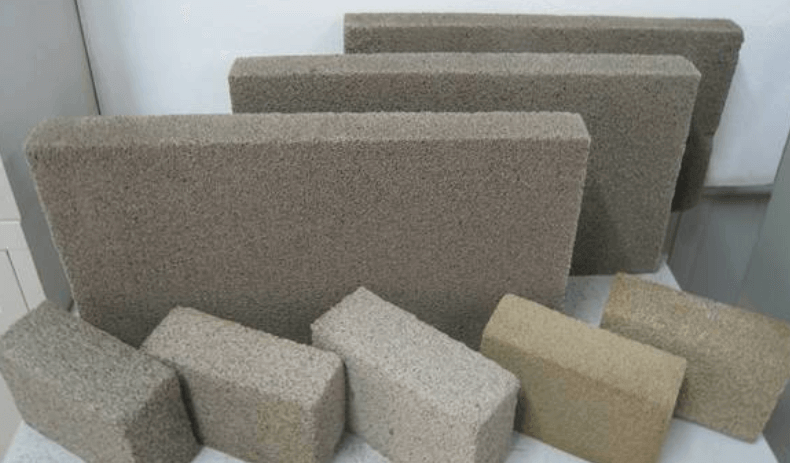
Advantages of Foam Concrete
- The foam concrete or lightweight concrete mix doesn’t settle. So, it needn’t bother with any compaction.
- The extra weight is diminished since it is light weight concrete.
- Under the fresh state of construction, the foam concrete has uninhibitedly flowing consistency. This property will help in totally making up for the shortcomings.
- The foam concrete or lightweight concrete design has good disseminating capability and load spreading.
- Foam concrete or lightweight concrete does not force critical lateral loads.
- It has a water retention property.
- The foam concrete or lightweight concrete groups are less difficult to make and for that control and quality check are handily done.
- The foam concrete has higher protection from thawing and freezing.
- It has a quicker work fruition and non-perilous.
- It is cost viable and very less upkeep.
Disadvantages of Foam Concrete
- In the mixed material the water presence makes the foamed concrete or lightweight concrete exceptionally delicate.
- It gives difficulty in wrapping up.
- It takes a longer time for mixing.
- With the expansion in density, the flexural strength and compressive strength diminishes.
Hempcrete Blocks and its Advantages and Disadvantages